O-Ring-Dichtungen sind der Standard in nahezu allen Industrie- und Anwendungsbereichen. Eingepasst in Dichtungsnuten erlauben sie eine einfache Montage und einen zügigen Austausch, sobald sie Anzeichen von Verschleiß zeigen. Was für statische Dichtungen – Dichtungen, die nicht bewegte Teile dichten – ein unbestrittener Vorteil ist, kommt bei dynamischen Dichtungen – Dichtungen für bewegte Teile – schnell an seine Grenzen. Dies im Besonderen, wenn es um anspruchsvolle Anwendungsbereiche mit hohen Anforderungen an Dichtungsleistung und Langzeitstabilität geht.
Dies gilt für viele Einsatzbereiche von Vakuumventilen. Sie fordern exzellente Dichtungseigenschaften auch bei hohen Differenzdrücken, ein gutes Dämpfungsverhalten, um Stöße speziell bei wiederholten, schnellen Schließbewegungen zu vermeiden, sowie hohe Langzeitstabilität, um Ausfallzeiten durch Wartung zu minimieren.
O-Ringe in solchen dynamischen Dichtungsbereichen müssen also einiges leisten. Wenn beispielsweise sehr große O-Ringe verwendet werden, neigen diese zum Verdrehen, was ihre Dichtungsfähigkeit einschränkt. Darüber hinaus geht mit O-Ring-Nuten die Gefahr einher, dass sich bei Vakuumventilen eingeschlossene Gasvolumina bilden, d. h. Bereiche unter dem O-Ring, die vom übrigen Prozess und damit von Druckänderungen abgeschottet sind. Diese Volumina bergen ein Risiko. Wenn z. B. der Umgebungsdruck prozessbedingt sinkt, steigt die Druckdifferenz zum Druck in diesen Bereichen. Der Differenzdruck kann so groß werden, dass der O-Ring aus der Nut gedrückt wird, was die Dichtungseigenschaften negativ verändert – bis zum Totalverlust der Dichtungseigenschaften. Vakuumventile mit dynamischen O-Ring-Dichtungen besitzen deshalb in der Regel spezielle O-Ring-Nuten, die dem entgegenwirken.
Haftdichtungen weisen diese Probleme nicht auf, da sie unmittelbar auf der Oberfläche eines Schließtellers fixiert sind. Die direkte Befestigung hat zudem den Vorteil, dass der gesamte für die Dichtung verwendete Elastomer-Werkstoff in den Dichtungsprozess einfließen kann. Hingegen muss bei einer O-Ring-Lösung ein Teil des Materials verwendet werden, um die Dichtung in der Nut zu halten.
Da Elastomere in Vakuumprozessen generell eine Quelle für Partikel und Ausgasungen sind, bedeutet weniger Materialeinsatz auch weniger Partikel und Ausgasungen. Haftdichtungen bestehen im Durchschnitt aus 35% weniger Material als vergleichbare O-Ring-Lösungen.
Weil bei der direkten Bindung das gesamte Material für die Dichtungsfunktion verwendet wird, lässt sich mehr Einfluss auf die Gestaltung der Dichtungseigenschaften nehmen. Das bedeutet, dass Haftdichtungen von der ersten Berührung mit dem Dichtungssitz bis zur endgültigen Position an der Dichtfläche maßgeschneidert werden können. Durch Veränderung der Höhe und Breite der Dichtung, z. B. von einer spitzen zu einer flachen Pyramidenform oder durch Abrundung der Spitze in unterschiedlichen Radien, kann die Dämpfungswirkung der Dichtung beim Schließen des Ventils gesteuert werden. Ebenso kann das Design das Öffnungsverhalten beeinflussen. Beispielsweise lässt sich bei großen Differenzdrücken durch das Design der Haftdichtung in Ergänzung zur Ventilsteuerung ein Öffnungsdruckimpuls dämpfen oder ganz vermeiden. Dies ist primär Relevant für Vakuumregelventile oder allgemein für Ventile mit mechatronischem Antrieb. Da hier mit entsprechend gestalteten Haftdichtungen bei einer geregelten leichten Minderung des Schließdrucks kleine, dosierte Volumenströme zugelassen werden können, die eine Druckveränderung dämpfen. Dies erhöht die Regelqualität und das regelbare Leitwertspektrum der Ventile.
Bei Haftdichtungen werden, ebenso wie bei O-Ring-Dichtungen, verschiedene Elastomere mit unterschiedlichen Eigenschaften eingesetzt, um verschiedenen Prozessbedingungen standzuhalten. Hierzu gehören aggressive Chemikalien, hohe oder niedrige Temperaturen oder andere anspruchsvolle Bedingungen.
Für Haftdichtungen entsteht damit die Herausforderung, diese Werkstoffe in immer gleicher Haftqualität mit der Telleroberfläche zu verbinden. Da aber die Elastomer-Materialien in ihren Bindungseigenschaften zum Teil stark variieren, können nicht alle mit der gleichen Technologie gebunden werden. VAT verwendet deshalb mehrere chemische und physikalische Haftmethoden.
Bei der chemischen Haftung wird ein Haftmittel zwischen dem Dichtungsmaterial und der Metalloberfläche des Tellers aufgebracht. Die Herausforderung besteht darin, ein Haftmittel zu finden, das die gleiche chemische und physikalische Beständigkeit und dasselbe Alterungsverhalten aufweist wie der Dichtungswerkstoff selbst. Ferner darf die Haftleistung die Dichtungsleistung des Dichtungsmaterials nicht unterschreiten. Sonst würde die Haftung zur Schwachstelle und die Lebensdauer der Dichtung bestimmen, statt wie erwartet das Dichtungsmaterial.
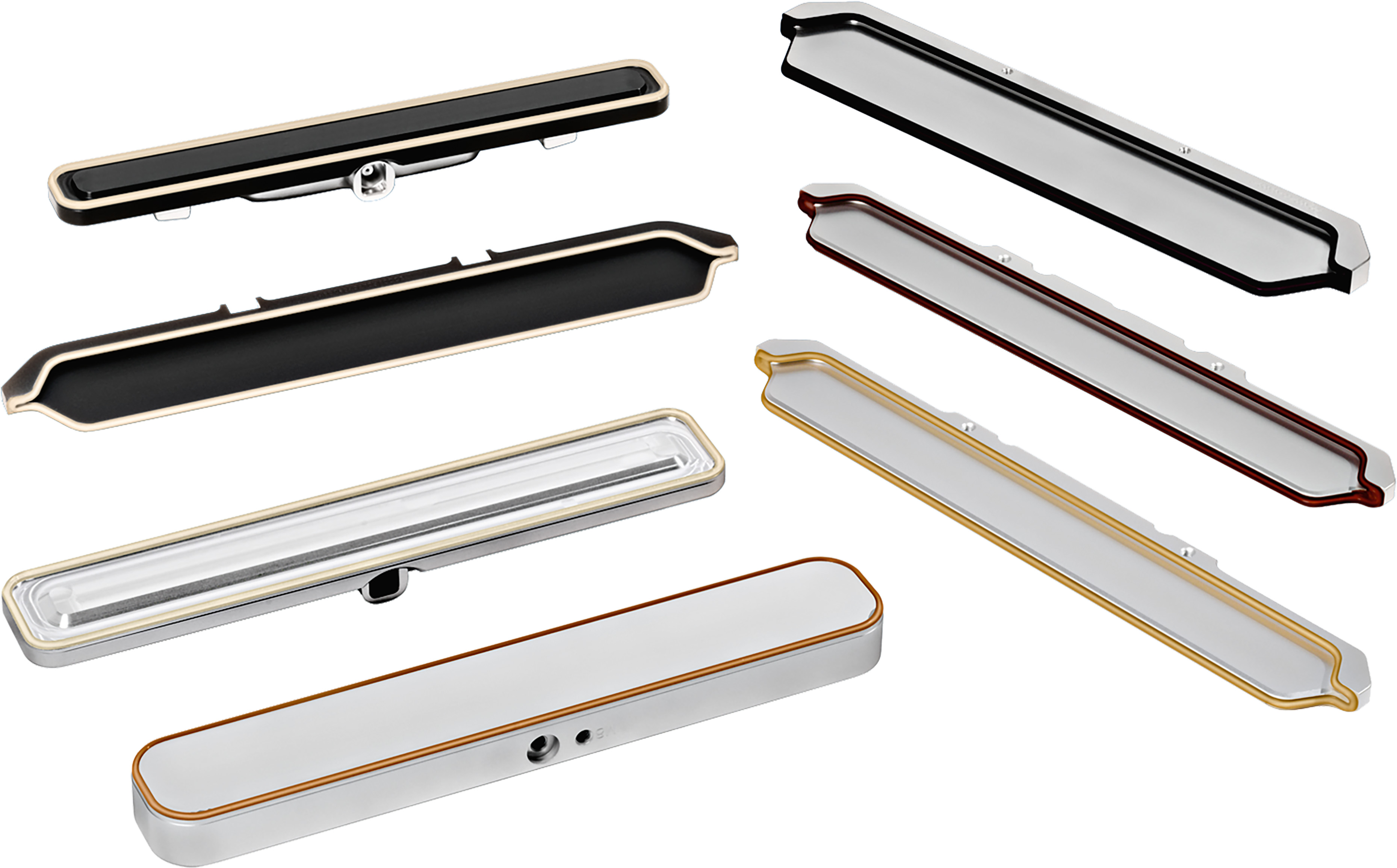
Daher nutzt VAT eine über Jahre aufgebaute umfangreiche Datenbank zu Dichtmaterialien und Haftmitteln sowie deren Kombination unter verschiedenen Prozessbedingungen. Die Hauptfunktion der Datenbank ist es, optimale Kombinationen für spezifische Bedingungen anzubieten. Darüber hinaus unterstützt sie dabei, Bereiche für Verbesserungen und die Entwicklung neuer Haftlösungen zu identifizieren.
Des Weiteren wächst die Bedeutung der physikalischen Haftung als Alternative zur chemischen Haftung. Die physikalische Haftung funktioniert, vereinfacht gesagt, wie ein Klettverschluss, bei dem sich eine Seite in die andere Seite oder beide Seiten ineinander verhaken. Die Herausforderung besteht darin, dass im Gegensatz zum Klettverschluss unterschiedliche Materialien mit deutlich unterschiedlichen Eigenschaften in Bezug auf Elastizität und Bruchverhalten aufeinandertreffen. Die Entwicklung einer Verbindung, die einem zuverlässigen Klettverschluss nahekommt, erfordert daher einige spezielle Kenntnisse. So ist z. B. eine angestrebte optimale Verzahnung darauf ausgelegt, eine dauerhafte statt einer wiederablösbaren Verbindung zu schaffen. Und diese Verbindung soll so beständig sein, dass auch bei starker dynamischer Beanspruchung und bei hohen Differenzdrücken die Dichtungseigenschaften über die Lebensdauer konstant bleiben.
VAT hat ein eigenes Entwicklungsteam, das sich mit der Erforschung und Entwicklung dieser Hafttechnologie befasst. Deren Hauptvorteil: Im Gegensatz zur chemischen Haftung braucht es kein drittes Material, kein Haftmittel.
Der Schwerpunkt der Entwicklungsarbeit liegt allerdings nicht nur auf verbesserter Haftung zwischen Dichtungsmaterial und Oberfläche des Ventiltellers. Das Team befasst sich auch mit der anderen Seite, dem Dichtungssitz. Die Dichtungsleistung von Haft- wie von O-Ring-Dichtungen wird nicht nur durch die Form und Auswahl der Dichtungsmaterialien und deren Befestigung auf dem Schließteller bestimmt. Die Wechselwirkung mit dem Dichtungssitz oder, genauer gesagt, mit der Oberfläche und dem Material des Dichtungssitzes spielt ebenfalls eine Rolle. Daher ist das Oberflächendesign des Vakuumventilsitzes, ein weiterer integraler Bestandteil der Konstruktion von Hochleistungsdichtungen und insbesondere von hochleistungsfähigen Haftdichtungen.
Hier besteht die Herausforderung darin, das richtige Gleichgewicht zwischen Dichtungsleistung einerseits und Vermeiden eines Verbindungsverhaltens oder Klebens andererseits zu finden. Bei einer sehr effektiven Dichtung füllt der Elastomer-Werkstoff alle Mikrovertiefungen, die sich auf der Oberfläche des Dichtungssitzes befinden, nahezu vollständig aus. Je besser sich aber der Elastomer-Werkstoff mit der Oberflächenrauigkeit des Dichtungssitzes verbindet und somit besser dichtet, desto mehr neigt er dazu, an der Oberfläche zu kleben, was wiederum die Dichtungsleistung einschränkt. Um das zu vermeiden, wird durch eine spezielle Oberflächenveredelung die Rauigkeit und damit die Anzahl der Mikrovertiefungen sehr stark reduziert. Dies ist jedoch keine vollständige Lösung, da jedes Elastomer-Material selbst eine gewisse „Rauheit“ aufweist, d. h. es hat selbst kleinste Vertiefungen und Erhöhungen an seiner Oberfläche. Wenn nun die raue Elastomer-Oberfläche auf eine glatte Sitzoberfläche trifft, nimmt zwar das Verbindungsverhalten oder Kleben ab, aber die bestehenden „Lücken“ werden nicht vollständig geschlossen, selbst wenn die Dichtungsfläche vergrößert wird, z. B. durch erhöhten Druck auf die Dichtung oder durch das Design. Es gilt also, die Seiten so zu gestalten, dass sie maximal formschlüssig sind, ohne dass es zu einem Haftverhalten kommt – und zwar ohne den Materialeinsatz zu erhöhen und ohne die Dichtung dynamisch zu überpressen. Beides hätte negative Auswirkungen: Verminderte Dichtungslebensdauer und erhöhte Gefahr von Partikelimmissionen.
Eine weitere wichtige Dimension bei der Gestaltung von Haftdichtungen ist die Temperatur. Grundsätzlich sind die eingesetzten Elastomer-Werkstoffe immer für bestimmte Temperaturbereiche optimiert. Trotzdem ist auch innerhalb des definierten Temperaturbereiches zentral, wie eventuelle Temperaturveränderungen auf die Dichtung wirken, ob langsamer Wandel oder kurze Temperaturspitzen. Das „Temperaturprofil“ eines Prozesses, d. h. speziell die Wirkung von Temperaturveränderungen an der Dichtung über die Zeit und in Relation zur dynamischen Belastung der Dichtung, ist ganz entscheidend für die Leistung und Lebensdauer der Dichtung. Die Temperatur verändert das Elastomer-Verhalten auch im zugelassenen Temperaturbereich. Dichtungen werden, vereinfacht gesagt, weicher oder härter. Entscheidend ist dabei nicht nur, dass sie es tun, sondern auch wann. Wenn die dynamische Dichtungsleistung am meisten gefordert ist, muss die Temperatur stimmen. Das bedeutet: Schließvorgang und Dichtvorgang sollten immer im optimalen Temperaturbereich ablaufen, nicht zuletzt, um eine Freisetzung von Partikeln zu minimieren.
Bei der Dichtungsauswahl muss deshalb neben den chemischen Rahmenbedingungen und den maximalen und minimalen Temperaturen des Prozesses darauf geachtet werden, welches Temperaturprofil vorliegt. Ist das Profil bekannt, kann gegebenenfalls der Einsatz passiver oder aktiver Kühl- oder Heizmaßnahmen eine Dichtungsleistung nachhaltig verbessern.
VAT hat diese Herausforderung beim Design von Haftdichtungen bereits für viele Anwendungsbereiche sehr erfolgreich gemeistert und damit eine Vielzahl von Kunden zu einem Umstieg auf Haftdichtungen motiviert. Dies im Besonderen, wenn es um hohe Anforderungen an die Langlebigkeit und ein stabiles, zuverlässiges Dichtungsverhalten geht. Nichtsdestotrotz sieht das VAT-Entwicklungsteam weiterhin großes Potenzial, um die eingesetzte Technologie noch weiter an unterschiedliche Prozessbedingungen und Anwendungen anzupassen.